
The lower M3 x 20mm screw also holds the fan shroud in place so be sure to remove this too.Ĥ. The top M3 x 14mm and the lower M3 x 20mm. Next, remove the two screws on the right side of the heatsink fan. Leaving the fan dangling can damage the wires.ģ. Make sure you do not stress the fan wires, they are very fragile. Tuck the fan between the belt and the rod on the X-axis. You should still be able to follow this guide in the same way, although some illustrations may vary from what you have in front of you.Ģ. You may find you have the early MK3 style upright fan on your extruder. Remove the two M3 x 20mm screws holding the part cooling fan in place. All MK3 Prusa Printers are 24V as standard.Ĭheck out our Blog if you are unsure on whether you need a 12 or 24V Revo Six:ġ. You should also place a cloth or piece of fabric over your heatbed to give it some protection in case you drop something onto it.ĭouble-check your printer before buying 12V or 24V. You should also ensure there is no filament loaded and that the printer is unplugged from the power source. Please move your extruder to roughly the centre of your bed and around 100mm above the build plate before starting this upgrade, this will give you easier access to the extruder. If you have an MK2/2.5 you can still follow this guide but you may want to refer to the Prusa documentation for extruder disassembly as some aspects will vary.
Prusa fan shroud upgrade#
Please note, your printer may vary from the one illustrated in this guide, depending on the model and your own upgrade choices. You should read through the whole guide before attempting the upgrade to ensure you understand exactly what is required to complete it successfully. You will also need Revo Six or Revo Six MK3 Edition. This is a complete upgrade guide suitable for an original Prusa MK3, MK3S, and MK3S+. This may impact performance or cause issues.Prusa released a new firmware 10/01/23 that has the potential to cause temperature issues with the Revo Six, Please refrain from upgrading for the time being until we can verify stability.įor the time being, firmware 3.11.0 is the last known stable firmware for use with Revo HotEnds.īefore upgrading your Prusa i3 with Revo Six please read the following safety cautions. Keep in mind that printing a lot of ASA in an unventilated enclosure can cause the fan shroud and/or extruder plastic parts to deform over time. This will create a wall around the object and keep the model slightly warmer, mitigating the warping. If you don’t have an enclosure, there’s one simple alternative: in PrusaSlicer, set the skirt value as high as possible. The bed should be heated to at least 100 ☌, and the printer should be inside an enclosure to keep a higher ambient temperature. ✖ Partially hygroscopic (absorbs moisture)ĪSA is suitable for outdoor use and for making technical parts. ✔ Possibility of acetone smoothing and gluing ✖ An enclosure is necessary for printing large parts ASA can be easily sanded both wet and dry. Another disadvantage is that ASA releases potentially dangerous fumes during printing - this means you should keep your printer in a well-ventilated area.
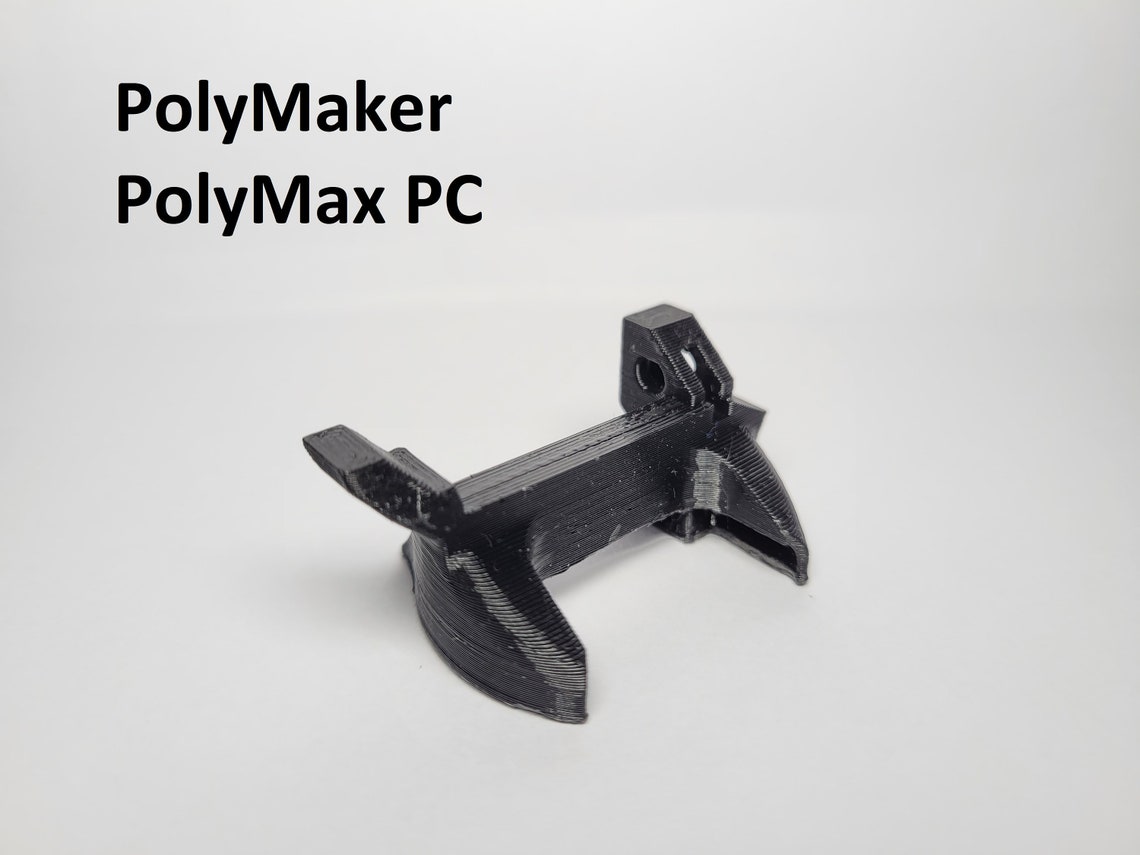
The main disadvantage of ASA is significant warping caused by temperature differences between the model and its surroundings. This gives the model not only great looks but also different mechanical properties (see our article about chemical smoothing). Another great advantage of ASA is its solubility in acetone vapors, which can be used to make a smooth and glossy finish. See for example our MK3S printer fan shroud. ASA is a tough and resilient material that is, thanks to its UV and temperature resistance (up to 93 ☌), suitable for outdoor use and for making technical parts. Compared to ABS, ASA is more UV resistant, warps less, and doesn’t smell as much. DescriptionĪSA (Acrylic Styrene Acrylonitrile) is a technical material that is considered a successor to ABS. Heatbed: Use the smooth or powder-coated PEI sheet with a glue stick.
